1.押出ブロー成形の課題
押出ブロー成形では、ダイから押出したパリソンを使用して成形を行うため、成形品の板厚は、パリソンの延伸に依存し、成形品形状によっては、延伸が不均等となり、板厚差が生じてしまう為、押出ブロー成形を用いて成形を行う場合、設計段階で成形に伴う板厚分布を考慮して、成形品の重量を算出する必要がある。
本事例では、BlowViewを用いて、押出ブロー成形時の成形品の重量を算出すると共に、押出ブロー成形のパリソン板厚を可変する機構を利用する事による成形品重量の変化を確認し、成形可能な成形品重量を算出する。
2.押出ブロー成形解析モデル
図1に示す40ℓタンクを押出ブロー成形を用いて最小板厚を2.0mmとして成形を行う。
最小板厚2.0mm一定とした場合の重量を表1に示す。
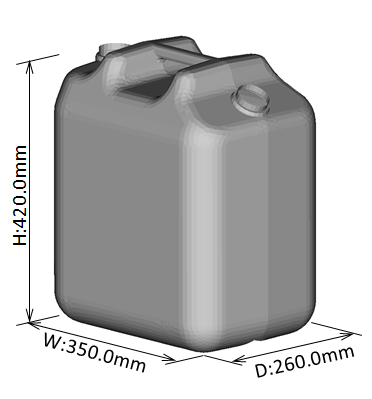
表1.均一板厚時の設計重量
板厚(mm) | 重量(Kg) |
2.0 | 1.11 |
図1.40ℓタンク
3.パリソン押出条件
本事例では、以下の条件で押出ブロー成形した成形品の重量をBlowViewで算出する。
① 成形品の最小板厚を2.0mmとする。
② φ160*1の押出ダイを用いて、パリソン押出方向をH、型分割をD方向とする。
*1: ダイ径は、スウェル比を1.4(一般的な経験値)として、パリソンの折幅が350mmになるサ イズとした。
パリソン板厚を変化させる機能として、押出ダイの開口率を可変させパリソンの押出方向で板厚変更する機構(VWDS)と押出ダイの外周部を扁平させパリソンの円周方向で板厚変更する機構(PWDS)がある。
本事例では、以下の手順で成形条件を調整して成形品の重量を算出し、比較を行う。
1) VWDSを一定とした条件
2) VWDSを用いて、成形品の板厚差を低減させた条件
3) VWDSとPWDSを用いて、成形品の板厚差を低減させた条件
尚、VWDS(ダイ開口率調整機構)及び、PWDS(ダイ扁肉調整機構)を図2、3に示す。
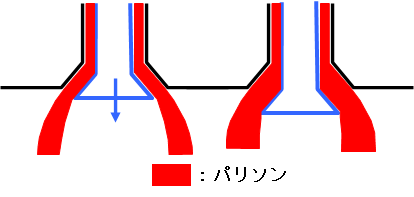
図2.VWDS:ダイ開口率調整機構
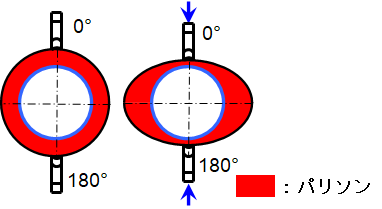
図3.PWDS:ダイ偏肉調整機構
また、VWDS及びPWDS条件は、図4に示す、VWDS一定条件でのパリソンコントロールポイント位置と同条件の板厚分布から、図5に示す、VWDS変更条件、及びVWDS+PWDS変更条件を設定した。
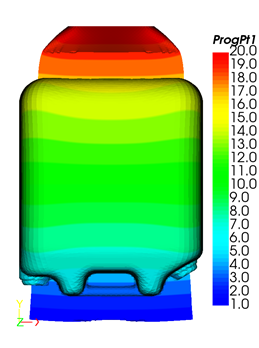
図4.VWDS一定条件パリソン
コントロールポイント
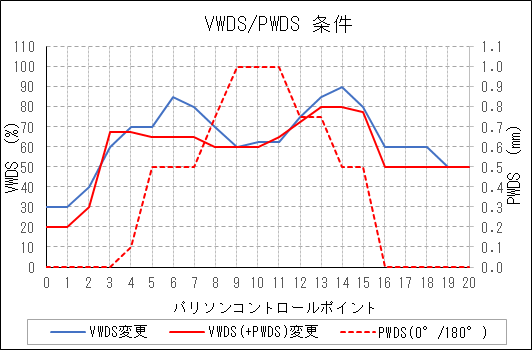
図5.VWDS&PWDS条件
4.BlowView解析結果
4-1.VWDS一定条件
図6.VWDS一定条件:パリソン押出&ブローアップ時 板厚変化
成形品形状で最小板厚(2.0mm)以上となるVWDS(一定)条件でパリソンを成形した。
・パリソン板厚
パリソン板厚は、10.0mm~11.0mmとした。
・成形品肉厚
上記のパリソン板厚であれば、最薄肉部でも2.0mm以上で成形可能。成形品中央部では、円周方向及び押出方向とも、パリソン表面-金型キャビ面との距離に差があり、中央部と外周部に板厚差(5.0mm程度)が生じる。
4-2.VWDS変更条件
図7.VWDS変更条件:パリソン押出&ブローアップ時 板厚変化
VWDS一定条件で、板厚差が生じている部位に対して、VWDS条件を調整して、パリソン押出方向に板厚差を設定した。
・パリソン板厚
成形品の上下角部の間に相当する部分を変更し薄肉化した。
同様に上下角部の外側部に相当する部分を変更し薄肉化した。
(成形品タンクの上下面に相当する範囲)
・成形品肉厚
上記のパリソンにより、成形品中央部の円周方向及び、押出方向の板厚差が低減(5.0mm⇒2.5mm)出来る。
4-3.VWDS+PWDS変更条件
図8.VWDS+PWDS変更条件:パリソン押出&ブローアップ時 板厚変化
更に成形品の板厚差を低減する為、成形品中央部に該当する範囲でPWDSを利用して、パリソン円周方向に板厚差を設定した。
・パリソン板厚
成形品中央部に相当する範囲でPWDSを利用する事で、円周方向に対して、成形品中央部に該当する範囲を更に薄肉化した。
・成形品肉厚
上記のパリソンにより、成形品中央部の板厚を薄くする事で板厚差が更に低減(2.5mm⇒2.0mm)出来る。
4-4.成形品比較結果
各条件で成形した成形品の板厚分布を図9に示し、各条件での成形品重量の比較を表2に示す。
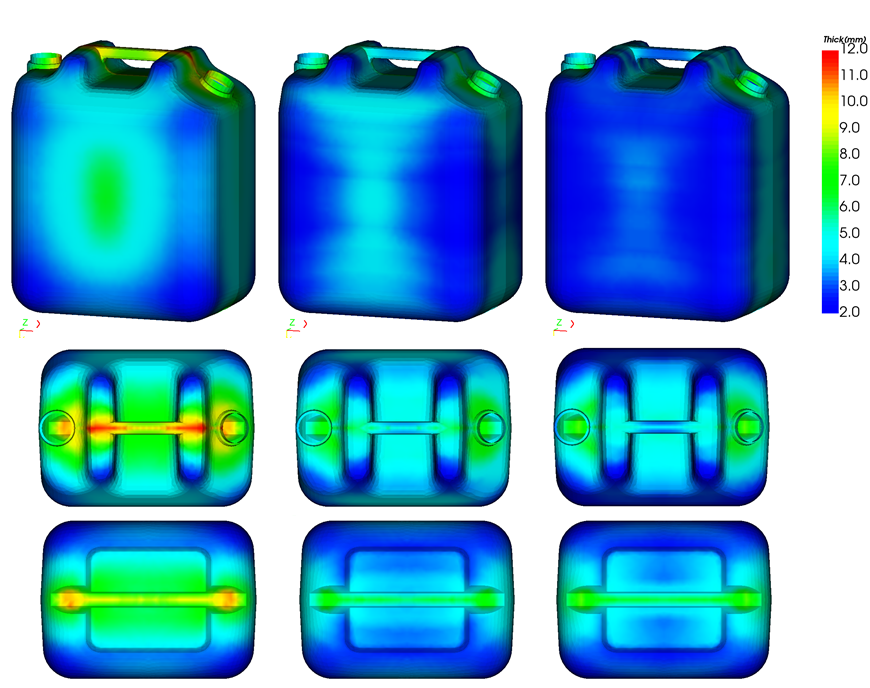
VWDS一定条件
VWDS変更条件
VWDS+PWDS変更条件
図9.各条件での成形品板厚分布比較
表2.各条件での板厚分布及び成形品重量
VWDS一定条件 | VWDS変更条件 | VWDS+PWDS変更条件 | |
平均板厚(mm) | 4.45 | 3.46 | 3.21 |
最小板厚(mm) | 2.06 | 2.00 | 2.04 |
最大板厚(mm) | 12.01 | 7.25 | 7.57 |
成形品重量(kg) | 2.47 | 1.92 | 1.78 |
2.0mm一定板厚タンク (1.11㎏)との重量差 |
1.36 | 0.81 | 0.67 |
5.まとめ
BlowViewを利用する事で、以下の事が確認出来る。
➀ 設計段階で生産に伴う板厚分布を反映した製品重量
(一定板厚に対して、最大+1.36Kgとなる。)
➁ 成形条件に伴う成形品の重量変化
(条件調整により、+0.67Kg程度に抑える事が可能。)
➂ 成形に使用するダイサイズや成形条件など設備対応の可否
以上の様に、BlowViewを利用する事で、設計段階で成形品の板厚分布や重量及び、成形機の仕様や成形条件など生産工程も含めて、品質やコストなどを検討する事が出来る。